3 Steps to Selecting Wash-Down Cordsets for Food & Beverage Plants
If you design industrial networks for food and beverage processors, or if you are an engineer in such a facility, you know that the cost of downtime is high. In fact it’s estimated that if a cabling system fails, the repair and labor costs alone could be 15 to 20 times the cost of the connector or cable itself -- if they can even be fixed at all. Downtime can reach overall costs of $20,000 to $30,000 per hour.
Not only are downtime costs high, operating conditions in these industries are some of the harshest around. That’s in large part because cleanliness and food safety are of paramount importance. Equipment must operate at top capacity even though it is subject to high pressure wash-downs, caustic cleaners, vibrations and extreme or varying temperatures.
What then are the guidelines for specifying or selecting the cordsets used to connect automated systems in the food and beverage industry? Let’s find out.
Wash-down cordsets help food and beverage processors achieve reliability and cleanliness objectives.
1. Know the Advantages of Wash-down Cordsets over Hardwiring
Up to now, the high focus on cleanliness has meant that food and beverage plants have primarily used hardwiring to connect sensors and actuators to central control panels. This has been done because cable and control boxes are available that can withstand the physical, chemical and temperature stresses that are part of the manufacturing and cleaning processes.
The disadvantages of hardwiring are that installation is expensive, requiring the work of a specialized electrician, and that hardwiring has a high risk of failing unexpectedly. If a specialized electrician isn’t available, these situations can last several hours, if not days – and often at the worst possible time, such as at the height of production. The productivity and material losses caused by this downtime can lead to even higher costs than planned downtime.
Thus the first guideline in selecting or specifying cordsets is to thoroughly evaluate using wash-down cordsets. These are sets of cables where one end of each cable is pre-installed with a connector at the factory. Both the cable and the connector are industrially hardened to meet food and beverage requirements.
Wash-down cordsets have the advantage of streamlining initial installation and replacement. Technicians, rather than specialized electricians, can quickly and easily attach cables to receptacles on a sensor at one end of a system and the control cabinet at the other end – and do it in as little as 15 or 20 minutes. This dramatically lowers the risk and cost of unplanned downtime.
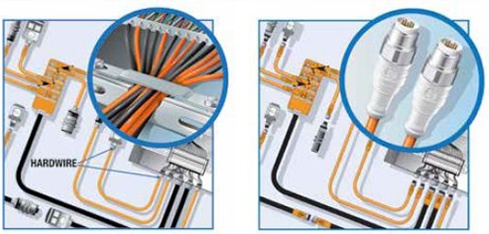
Traditional hardwiring is shown on the left and easy-to-install wash-down connectors on the right.
2. Select the Right Wash-down Cordsets for the Environmental Requirements
Wash-down cordsets are designed and built to withstand all the harsh conditions typical of food and beverage operations. Investigate the ratings and certifications needed for your application, keeping in mind:
- Integrity: Vibration-proof, able to withstand cleaning with high-pressure equipment and have smooth surfaces to avoid bacteria and residue build-up
- Impermeability (ECOLAB Certified): Resistance to aggressive chemicals and cleaning agents to avoid degradation
- Temperature Tolerant and Fire Resistant (UL Approval): UL certified means that the cordsets are suited for temperatures ranging from-40° C to 105° C and that they guard against the outbreak and spreading of fires.
- Industry Ratings:
- IP67 – waterproof
- IP68 – waterproof submersion
- IP69 – can withstand cleaning with high-pressure equipment
3. Pay Particular Attention to the Connector Component and to Factory Testing
When investigating wash-down cordsets, select ones with high quality connectors:
- Installation: Connectors should be easy to install with standardized M8 or M12 connection technology
- Reliability: Connectors should be equipped with gold-plated crimp contacts for reliable data transfer
- Flexibility: Connectors should provide options for a variety of different poles
Finally, look for wash-down cordsets that come with pre-installation factory testing. This dramatically reduces troubleshooting during installation, expedites the time it takes to get systems up and running and helps ensure that the cordsets perform consistently.
Selecting Food and Beverage Connectivity that Avoids Costly Downtime
When selecting wiring solutions for food and beverage systems, the initial higher investment in wash-down cordsets is usually more than offset by savings in wiring installation costs, maintenance costs and downtime losses.
The wash-down cordsets selected need to have the right environmental ratings for the application in question and high quality connectors. Finally, pre-installation factory testing contributes to fast start-up time and consistent performance.
To learn more about wash-down cord set solutions, download the white paper available below.
You might also be interested in learning about IP69K rated distribution boxes which can be washed down using the same high-pressure equipment as is used on wash-down cordsets.
What challenges do you face with selecting connectivity solutions for food and beverage applications? I look forward to hearing from you.