Manufacturing IT—Separate the Industrial Network from the IT Network
The flat network design had been controlled by the IT department which initially did not understand how the good practices it used to manage the enterprise network were disrupting the plant floor network.
As the demand for real-time information has increased, more and more IT professionals are becoming involved with manufacturing networks. If you are one of those people, or if you are an engineer who wishes IT understood your operational network requirements, then the Johnson Controls story that follows may be helpful.
Enterprise IT and Industrial IT Are NOT the Same
Network strategies and objectives differ depending on the job. The IT department must place data integrity first. On the other hand, Just-in-Time (JIT) production facilities live and die by keeping manufacturing lines up and running in order to meet production quantity, quality and delivery demands.
At Johnson Controls there were three main challenges for the control engineers under the old flat network architecture:
- IT network scans sometimes consumed needed bandwidth at the wrong time. This could cause just enough of a delay to knock factory devices, which do not tolerate randomness in the delivery of time-critical signals, offline. The result was unplanned shutdowns that played havoc with tight manufacturing schedules.
- Network management was delegated to a 3rd-party operator. A Service Level Agreement (SLA) that suited the needs of the IT group governed the 3rd party's response. When a port address or other network detail needed to be changed, the IT coordinators had to submit a change order. Sometimes equipment failed or lines went down while orders were in process.
- IT coordinators and controls engineers sometimes spent hours troubleshooting network interruptions, a costly exercise when there is a factory schedule to maintain.
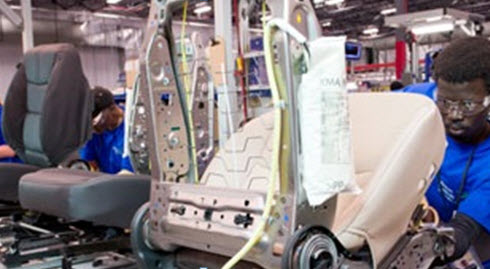
In order to keeps production of Johnson Controls' products running smoothly the plant floor network and the IT network had to be isolated from each other. Image courtesy of Johnson Controls.
Creating a Global Industrial Network Strategy
Part of the Johnson Controls' migration to a more robust industrial Ethernet infrastructure was to separate the IT network from the plant network. It also involved having an industrial firewall control the communications between the two networks. This solution was proposed by Joe Lavis, the IT manager in the Automotive Experience Group's IT Process Office, together with Kevin Hooks, the IT director for manufacturing, Supply Chain & Quality Systems.
The new network design was approved by management and has now been rolled out to the Johnson Controls' Northwood, Ohio, JIT plant. The same design will be rolled out to global facilities as new plants are built or when a major expansion with significant downtime is planned.
According to Lavis, the operational benefits of the new architecture are:
-
Higher availability through the a reduction of unplanned shutdowns.
-
Protection of production controls equipment from chatty office traffic and unannounced network scans, which have knocked devices offline in the past).
-
Increased network efficiency through reduced bandwidth consumption by multicast traffic, thanks to switch management features.
-
Improved security and granular control of messages being passed between the IT and plant networks by using an industrial firewall between the two networks.
- Controls engineers now have complete production network ownership, allowing them to manage it to meet and exceed manufacturing targets.
On the financial side, another benefit was being able to capitalize the new plant network equipment required since industrial switches and routers are designed to operate for long periods of time, up to 25 years.
Corporate IT and Control Engineer Cooperation Pays Off
This success of this Johnson Controls' project shows how IT can drive change that leads to better company results by understanding the unique requirements of industrial networks.
What are your thoughts on how IT and OT should work together? I look forward to hearing your comments.
Related Links